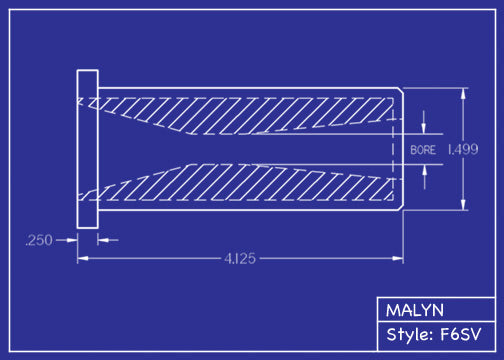
Venturi Sandblast Nozzles Vs Straight Bore Blast Nozzles
When it comes to sandblasting, the type of nozzle you use can make a significant difference in the efficiency and effectiveness of the process. Two common types of nozzles used in sandblasting are Venturi sandblast nozzles and straight bore blast nozzles. But what sets them apart? Let's dive into the differences between these two nozzle types.
What is a Venturi Sandblast Nozzle?
A Venturi sandblast nozzle is designed with a converging section followed by a diverging section. This design creates a constriction in the nozzle that accelerates the abrasive material, such as sand or grit, as it passes through. The accelerated abrasive material then exits the nozzle at high velocity, making it effective for removing tough coatings and rust from surfaces.
What is a Straight Bore Blast Nozzle?
On the other hand, a straight bore blast nozzle has a consistent diameter throughout its length. This design allows for a more focused and concentrated stream of abrasive material, making it ideal for precision blasting applications where accuracy is crucial.
Key Differences
One of the main differences between Venturi sandblast nozzles and straight bore blast nozzles is the velocity of the abrasive material. Venturi nozzles are known for their high-velocity output, which makes them suitable for removing heavy coatings and rust. In contrast, straight bore nozzles offer a more controlled and precise abrasive stream, making them ideal for intricate blasting tasks.
Additionally, Venturi nozzles are often preferred for applications that require higher productivity and faster blasting speeds. The accelerated abrasive material can cover a larger surface area in a shorter amount of time compared to straight bore nozzles.
Choosing the Right Nozzle
When deciding between Venturi sandblast nozzles and straight bore blast nozzles, it's essential to consider the specific requirements of your sandblasting project. If you need to remove thick coatings or rust quickly, a Venturi nozzle may be the best choice. On the other hand, if you require precision and control for delicate blasting tasks, a straight bore nozzle would be more suitable.
Ultimately, the choice between Venturi sandblast nozzles and straight bore blast nozzles will depend on the nature of your sandblasting project and the desired outcome. Both types of nozzles have their own unique advantages, so it's essential to select the one that aligns with your specific needs.
The introduction of venturi nozzles over thirty years ago is still considered the latest major advancement in nozzle technology.
You see up until the mid 1950's, all sandblasting nozzles were straight bore. They had a tapered converging entry, a parallel throat section, and a full length straight bore and straight exit. Over time, blast operators noticed that as the interior of these nozzles began to wear and erode away, a larger and more efficient blast pattern resulted. This observation led to the development of the venturi design.
A long venturi nozzle is characterized by having a long tapered converging entry, with a short flat straight section, followed by a long diverging end which widens as you reach the exit end of the nozzle. A long converging entry introduces the air and abrasive mix into the nozzle, then is constricted into a short flat straight section, and then forced out the flared exit end. Venturi nozzles can increase productivity by as much as 70% due to the larger abrasive pattern that results as well as due to the increase in velocity of the abrasive as it exits the nozzle. In fact, velocity (outlet speed) of the exiting abrasive can be nearly double that of a straight bore nozzle, and this is force that cleans a surface faster!
So if you are in the market looking to upgrade your operation, perhaps changing to a venturi nozzle might be a good place to start. More on that later...